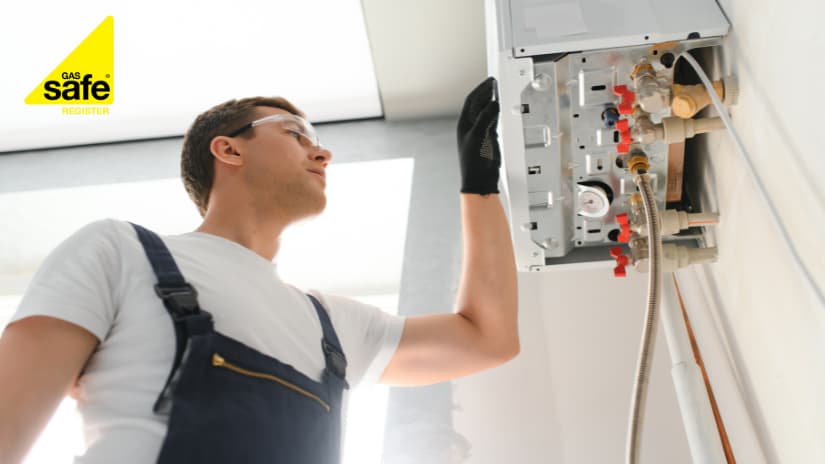
Health and safety are paramount in any profession, but they are particularly critical in fields involving technical expertise and hazardous materials, such as gas engineering. Gas engineers are essential in ensuring that domestic and commercial environments are safe for occupants. They are responsible for installing, maintaining, and repairing gas systems and appliances, which, if improperly managed, can pose significant health and safety risks. The consequences of neglecting these risks can be severe, resulting in accidents, injuries, or even fatalities. Therefore, understanding and implementing robust health and safety practices is not just a regulatory requirement but a moral imperative.
Gas engineers work in various settings, from residential homes to large industrial sites. Each environment presents unique challenges and hazards, ranging from exposure to toxic gases like carbon monoxide to the risks of working in confined spaces. The diversity of these settings requires gas engineers to be adaptable and knowledgeable about safety protocols specific to each context.
Gas engineers are highly regulated to ensure safety and efficacy. The Gas Safety (Installation and Use) Regulations 1998 are central to this regulatory framework. These regulations mandate that all gas engineers be listed on the Gas Safe Register to work legally in the UK. This registration ensures that engineers have the necessary qualifications and that their competencies are regularly updated to reflect the latest safety standards and technological advancements. Compliance with these regulations is not just about adhering to the law; it is about ensuring that all work undertaken meets the highest safety and quality standards, protecting the engineers and those who use the installations they service.
Gas Engineers
Gas engineers are vital to safely operating and maintaining fuel gas systems, ensuring these critical components function efficiently and safely. Their work encompasses a broad range of responsibilities and skills, highlighting the importance of their role in both domestic and commercial environments.
Responsibilities of Gas Engineers
Installation:
Gas engineers are responsible for installing new gas systems and appliances. This includes laying out gas pipelines and setting up gas boilers, heaters, and other gas-operated machinery. Their expertise ensures that installations comply with all safety standards and regulations, optimising safety and functionality.
Maintenance:
Regular maintenance is crucial to the longevity and safety of gas systems. Gas engineers conduct routine checks and servicing to ensure systems operate efficiently. This includes testing controls and safety devices, cleaning filters, and checking for leaks and corrosion.
Repair:
When gas systems malfunction, gas engineers diagnose issues and execute repairs. This might involve replacing parts, such as valves and thermocouples, or adjusting system settings to ensure optimal operation.
Differentiation Between Gas Engineers and Plumbers
While there is some overlap between the roles of gas engineers and plumbers, particularly in systems that involve water heating, their primary focuses are quite distinct:
Gas Engineers:
They specialise in installing, maintaining, and repairing gas lines, appliances, and equipment. They must be registered on the Gas Safe Register and are trained specifically in safety practices related to combustible gases.
Plumbers:
They focus on installing and repairing water and drainage systems. Some plumbers also work on heating systems, including boilers, but only Gas Safe, registered professionals can legally work on gas boilers.
Working Environments
Gas engineers operate in various environments, each presenting different challenges and requiring specific knowledge and skills:
Domestic Settings:
Gas engineers install and service home appliances like stoves, ovens, and central heating systems. Safety is paramount, as improper installation or maintenance can lead to gas leaks or carbon monoxide poisoning.
Commercial Settings:
Gas engineers may deal with larger, more complex systems in commercial premises, such as restaurants, hotels, and industrial plants. These might include industrial boilers, large-scale heating systems, and commercial cooking appliances. The complexity of these systems often requires specialised knowledge of commercial gas applications.
Emergency Services:
Gas engineers also provide critical emergency services, responding to reports of gas leaks or malfunctioning appliances. This aspect of their work requires high readiness and rapid response to prevent potential disasters.
Health and Safety Risks for Gas Engineers
Gas engineering, while essential, exposes workers to various health and safety risks that must be carefully managed to prevent accidents and ensure overall safety.
Chemical and Combustible Hazards
Carbon Monoxide Poisoning:
One of the most severe risks for gas engineers is exposure to carbon monoxide (CO), an odourless, colourless gas that can be lethal if inhaled. The incomplete combustion of natural gas produces CO and can accumulate in poorly ventilated areas, posing a significant danger to health. Symptoms of CO poisoning include headache, dizziness, nausea, and, in severe cases, unconsciousness or death.
Fire Risks:
Gas engineers work with flammable materials that can ignite under certain conditions. Improper handling of gas can lead to leaks, which may result in explosions or fires, especially in enclosed spaces or near ignition sources.
Gas Leaks:
Gas leaks can cause asphyxiation and increase the risk of fire and explosion. Natural gas displaces oxygen in the air, leading to suffocation if the area is not adequately ventilated.
Physical Risks
Manual Handling Injuries:
The physical nature of a gas engineer’s job can lead to various musculoskeletal injuries. These injuries often result from handling heavy or awkward objects, repetitive motions, or maintaining uncomfortable positions for extended periods.
Equipment-Related Injuries:
Using tools and machinery necessary for cutting, welding, and manipulating gas lines can pose risks such as cuts, burns, or eye injuries from flying debris. Proper personal protective equipment (PPE) and adherence to safety protocols are crucial to mitigate these risks.
Environmental Hazards
Confined Spaces:
Gas engineers often work in confined spaces such as underground vaults, storage tanks, or small utility rooms. These environments can be hazardous due to limited entry and exit points, poor ventilation, and the potential presence of toxic gases. Working in confined spaces requires special training and equipment to manage the increased risk of asphyxiation, explosion, and other injuries.
Variable Work Sites:
Gas engineers may work in diverse environments, each presenting unique challenges. Outdoor sites may expose workers to adverse weather conditions, which can affect the work’s safety. Indoor environments might involve working at heights, near live electrical systems, or in areas with old or deteriorating infrastructure.
Mitigating Risks
To address these risks effectively, gas engineers and their employers must implement robust safety measures, including:
Regular Training:
Keeping up-to-date with the latest safety protocols and hazard recognition.
Use of PPE:
Always wear the appropriate safety gear, such as gas masks, gloves, goggles, and helmets.
Proper Ventilation:
Ensuring adequate ventilation in all working environments to prevent the accumulation of gases.
Risk Assessments:
Conducting thorough pre-job safety assessments to identify and mitigate potential dangers.
Emergency Preparedness:
Having clear, practised procedures for responding to gas leaks, fires, and other emergencies.
Risk Assessments
Risk assessments are fundamental to health and safety, especially in fields involving inherent dangers such as gas engineering. They are a preventive measure and a legal requirement under UK health and safety laws.
Importance of Risk Assessments
The primary purpose of conducting risk assessments is to ensure the safety and well-being of everyone present at a worksite. The stakes are particularly high in gas engineering, where the risks include explosive gases, toxic substances, and high-pressure systems. Effective risk assessments help to:
- Identify potential hazards before they cause harm.
- Create awareness among workers and management about the risks associated with their tasks.
- Ensure sufficient measures are in place to control or eliminate identified risks.
- Minimise the likelihood of accidents and occupational illnesses.
- Comply with legal standards, thus avoiding penalties and protecting the company’s reputation.
Conducting a Risk Assessment
A risk assessment involves several systematic steps to identify hazards, analyse or evaluate risks, and determine appropriate ways to mitigate them.
Identify Hazards:
The first step is to walk through all work processes and environments to spot potential sources of harm. Hazards in gas engineering might include exposure to toxic gases, risk of fire or explosion, mechanical hazards from tools and equipment, and ergonomic risks from manual handling.
Decide Who Might Be Harmed and How:
Determine who is at risk, including gas engineers, other staff on-site, clients, and even the public, if the work is inaccessible areas. Understanding how these individuals might be harmed is crucial for planning safety measures.
Evaluate the Risks:
Assess the likelihood and severity of harm from identified hazards. This evaluation helps prioritise which risks need immediate attention and which can be more effectively managed with simple solutions.
Record Your Findings:
Documenting the findings and proposed safety measures is a legal requirement. This documentation should be clear and accessible to all employees involved in the operations.
Review and Update:
Risk assessments should not be static; they must be reviewed and updated regularly, especially when working practices, tools, or the work environment change.
Legal Obligations
Under UK law, particularly the Management of Health and Safety at Work Regulations 1999, employers must conduct risk assessments to manage health and safety risks effectively.
Legal obligations include:
- Conducting an adequate assessment of the risks to employees and anyone affected by their activities.
- Implementing appropriate measures to control identified risks.
- Providing information and training to employees about the risks and precautions.
- Keeping assessments and safety measures records, especially in organisations with five or more employees.
Failure to comply with these obligations can lead to legal consequences, including fines, liability claims, and damage to business integrity.
Personal Protective Equipment (PPE)
Personal Protective Equipment (PPE) safeguards gas engineers from daily hazards. PPE acts as the last line of defence against injuries and health risks, emphasising its essential role in the workplace.
Types of PPE for Gas Engineers
Gas engineers require specific types of PPE to protect against the unique hazards of their work environment:
Helmets:
Protect against head injuries from falling objects, bumps against fixed objects, or electrical hazards.
Gloves:
Different types of gloves may be required, including insulated gloves for electrical work, chemical-resistant gloves for handling hazardous materials, and cut-resistant gloves for working with sharp objects.
Eye Protection:
Safety goggles or face shields are necessary to protect against flying particles, chemical splashes, or intense light from welding operations.
Hearing Protection:
Earplugs or earmuffs are essential when working in environments with high noise levels, such as those generated by heavy machinery or during metal fabrication.
Respiratory Protection:
Respirators or breathing apparatus are required when working in confined spaces or inhaling toxic gases or fine particulates, which is risky.
Protective Clothing:
Fire-resistant clothing protects against heat and flames encountered during welding or in the event of a fire. Coveralls and boiler suits shield the body from minor spills, cuts, and abrasions.
Footwear:
Safety boots or shoes with steel toes and puncture-resistant soles are vital to protect feet from heavy objects, sharp materials on the ground, or electrical hazards.
PPE in Preventing Workplace Injuries
PPE is critical in minimising exposure to hazards that can cause workplace injuries or illnesses. By providing a barrier between the worker and the hazards, PPE effectively reduces the chance of accidents and the severity of injuries that may occur, thus:
- Enhancing safety when technological or administrative controls are not feasible.
- Providing emergency protection in high-risk situations, such as gas leaks or unexpected system failures.
- Increasing workers’ confidence, thereby boosting their efficiency and effectiveness on the job.
PPE Under Health and Safety Regulations
The provision and use of PPE in the workplace are covered under the Personal Protective Equipment at Work Regulations 1992 (as amended). These regulations mandate several responsibilities for employers, including:
Provision of PPE:
Employers must provide appropriate PPE to employees, free of charge, wherever there are risks to health and safety that cannot be adequately controlled by other means.
Assessment:
PPE must be carefully selected before use to ensure it is suitable for the intended purposes.
Maintenance and Storage:
Employers are responsible for maintaining, storing, and replacing PPE to ensure it remains in good working condition.
Training and Instructions:
Employees must be trained to use PPE, including how to wear it correctly and when necessary.
Training and Qualifications
Staying updated with the latest training and obtaining the necessary qualifications are crucial components of professional practice for gas engineers. These ensure that engineers comply with legal and safety standards and maintain the highest levels of competency and safety in their work.
Required Certifications and Training
Gas Safe Registration:
All gas engineers must be registered with the Gas Safe Register, the official gas registration body. This registration proves that an engineer is qualified to work safely and legally on gas appliances. It involves a rigorous assessment of the engineer’s ability to handle gas safely.
City & Guilds or NVQ Certifications:
Many gas engineers hold vocational qualifications such as NVQ (National Vocational Qualifications) or City & Guilds in heating, ventilation, and gas servicing technology. These qualifications are essential for foundational knowledge and skills in the trade.
ACS (Accredited Certification Scheme):
This certificate is mandatory for all individuals working with gas. It covers various aspects of gas safety and must be renewed every five years to ensure that the engineer’s knowledge and skills are current. The ACS Pathway to Core Domestic Gas Safety is a rigorous training and assessment program designed to equip candidates with a fundamental understanding of gas safety legislation standards, and best practices.
Ongoing Education and Training Updates
The field of gas engineering is continuously evolving due to technological advancements and changes in safety regulations. Continuous professional development (CPD) is therefore vital for:
Compliance:
Ensuring all practices align with the latest health and safety legislation.
Safety:
Keeping up with new safety techniques and tools that enhance workplace safety.
Efficiency:
Learning about new technologies and methods that improve the efficiency of gas systems.
Seminars, workshops, refresher courses, and subscriptions to industry publications can be used to achieve ongoing education.
Specific Courses Recommended
To remain at the forefront of the profession, gas engineers are encouraged to engage in specific courses that cover advanced topics as well as emerging technologies and regulations:
Combustion Performance Analysis:
Courses that teach how to check appliances’ combustion efficiency ensure that engineers can optimise systems to be safe and energy-efficient.
Energy Efficiency:
Understanding how to make systems more efficient saves costs and aligns with global sustainability goals.
Renewable Energy Solutions:
As the world shifts towards renewable sources, courses in solar thermal technology, heat pumps, and biomass heating systems are becoming increasingly relevant.
Health and Safety Executive (HSE) Courses:
These courses focus on broader health and safety aspects at work and are tailored to the risks associated with gas engineering.
Emergency Response Training:
Knowing how to respond to gas leaks and other emergencies is crucial given the nature of the work.
Auditing of Gas Work:
Gas work auditing is necessary to assess risk, ensuring gas appliances have been installed and serviced correctly.
ACS Extention of Scope:
ACS extension of scope adds additional appliance codes to your ACS certificate and allows you, upon completion, to work on these additional appliances within your Gas Safe status.
Legal Compliance and Industry Standards
Adherence to legal standards and industry regulations is crucial in gas engineering, where safety is paramount.
Overview of Legislation
The Gas Safety (Installation and Use) Regulations 1998:
These regulations are fundamental for gas safety in the UK. They set out the duties of gas engineers, including requirements for the safe installation, maintenance, and use of gas systems and appliances. The regulations mandate that all gas work must be carried out by Gas Safe registered engineers, ensuring that those handling gas operations are qualified and competent.
The Health and Safety at Work etc. Act 1974:
This Act provides the legal framework to promote, stimulate and encourage high health and safety workplace standards. It applies to all work activities, including those of gas engineers, and covers the responsibilities of employers and employees to ensure safety as far as reasonably practicable.
The Management of Health and Safety at Work Regulations 1999:
These regulations require employers to carry out risk assessments, make arrangements to implement necessary measures, appoint competent people, and arrange for appropriate information and training.
The Control of Substances Hazardous to Health Regulations 2002 (COSHH):
While more general, these regulations are relevant to gas engineers handling substances that could pose health risks, such as chemicals used in treating water within heating systems.
Health and Safety Executive Inspections and Audits
The HSE plays a critical role in enforcing health and safety legislation. It conducts inspections and audits to ensure compliance with laws:
Inspections:
Inspections can be routine or triggered by a specific incident or complaint. During an inspection, HSE officers ensure workplace safety measures are appropriately implemented and followed. For gas engineers, this might include verifying the correct use and maintenance of personal protective equipment, the safe use of gas equipment, and adherence to Gas Safety regulations.
Audits:
Audits are more detailed than inspections and involve a comprehensive review of an organisation’s adherence to safety laws. They assess the effectiveness of health and safety management systems, policies, and practices, ensuring they are both in place and effective.
Consequences of Non-Compliance
Failing to comply with gas safety laws and regulations can have serious consequences, including:
Legal Repercussions:
Non-compliance can result in prosecutions and severe penalties. For example, illegal gas work can lead to substantial fines and even imprisonment, mainly if it results in an accident or injury.
Financial Repercussions:
Beyond fines and legal costs, companies may face increased insurance premiums and potential damages claims. Non-compliance can also lead to costly disruptions in business operations.
Reputational Damage:
Legal issues, particularly safety failures, can damage a company’s reputation, affecting customer trust and business prospects.
Revocation of Licenses:
For serious breaches, individuals or companies can lose their Gas Safe registration, which is essential for legally working on gas systems and appliances.
Ensuring legal compliance helps avoid these adverse outcomes and contributes to the safety and well-being of workers and the public. Gas engineers and their employers must stay informed about changes in legislation and best practices to maintain compliance and uphold the highest safety standards in their industry.
Related Articles
- RIDDOR for Gas Engineers
- Open Flue Inspection and Testing for Gas Engineers
- F-Gas Regulations and their Impact on the HVAC-R Market
- Training Course Curriculum of MLPs for Gas Engineers
- Requirements for Boilers in Loft Spaces